g-Cueing | Innovative Design
With a combination of innovative hardware design and advanced algorithms, the Cranfield motion systems creates the sensation of acceleration in a compact, lightweight, inexpensive and energy efficient package. It provides high-fidelity g-cues indefinitely which cannot be achieved with any other system.
Our full motion system has a footprint of approximately just 1.8m x 2m and can be powered by a single mains supply socket.
Cranfield Simulation products are in use by teams in Formula 1 as well as many other manufacturers, driver training centres and individuals across the globe.
KEY FACTS
Cranfield Simulation is the only provider of simulators capable of providing the sensation of sustained motion.
Unique technology provides high fidelity motion cues with low latency and with no maximum duration.
Cranfield g-Cueing has been developed over a period of 30 years and utilises technology from our aerospace solutions.
With 4 modules of motion technology operating in 11 dof across all 6 axes, the highly accurate and almost instantaneous system provides an incredibly realistic driving sensation.
Our Technology
Our systems provide both onset and sustained high fidelity motion cues with low latency and no maximum duration. By triggering the body's vestibular system to make the brain believe the body is moving, we can reduce the overall sizing envelope, power requirements and cost of the simulator dramatically.
Our patented g-cueing system achieves this by applying pressure to the body using pneumatic modules positioned around the seat and safety harness. This simulates sustained acceleration, braking and cornering forces without the possibility of negative cues or wash-out.
By coupling g-cueing with our other systems designed in-house, we replicate the compression of the body under high g-forces, suspension travel of the vehicle under pitch, roll and heave, vibrations from the engine and track surface, and the limits of tyre traction during high speed cornering. These motion cues are provided to the driver through four layers of actuation, each adding their own cues to the driver.
When combined, our motion modules provide an incredibly immersive driving experience that is only challenged by industry leading driver-in-the-loop simulators.
Our motion cueing systems are fully modular, allowing you to select motion systems to suit your requirements or budget. Systems can also be added at a later date. Additionally, it is possible to integrate any of our systems with static or motion simulators you may already have.
Read more below to discover details about each of our modules.
Suspension
In each corner of the platform, a linear actuator is fitted to simulate a typical suspension arrangement of a spring and damper.
Working independently or simultaneously, the actuators provide accurate feedback from the track surface from the simulation software enabling the driver to feel every bump, rumble, and surface change.
The actuators can also pitch the whole simulator forwards and backwards to simulate acceleration and braking, as well as side to side for body roll. Able to accelerate up to 1G and replicate frequencies up to 100Hz, the system can simulate any road surfaces, suspension movement, and vehicle vibration to unprecedent accuracy.
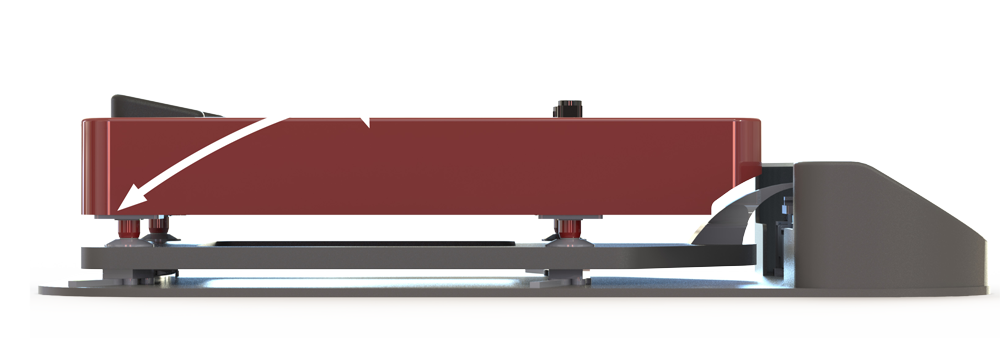
Powered By
g-Seat
On track, accelerations and the sensation of g-forces are transmitted to the driver through the seat. As the largest surface area that the body is in contact with, accurately reproducing these sensations in the simulator is highly important in training and implementing correct car control.
Developed from our military fast-jet simulators for fighter pilots, our g-seat is lined unique pneumatic pressure modules to provide sustained g-cueing. Multiple airbags in the seat and the harness expand and contract to provide localised and sustained pressure, simulating the g-forces felt when cornering, braking and accelerating indefinitely.
This system can be retrofitted into many types of seats, therefore existing simulators can also receive the benefits of Cranfield technology. The low mass of the pneumatic system also means that it can be added to existing weight sensitive motion platforms such as 6-Dof systems without degradation in performance.
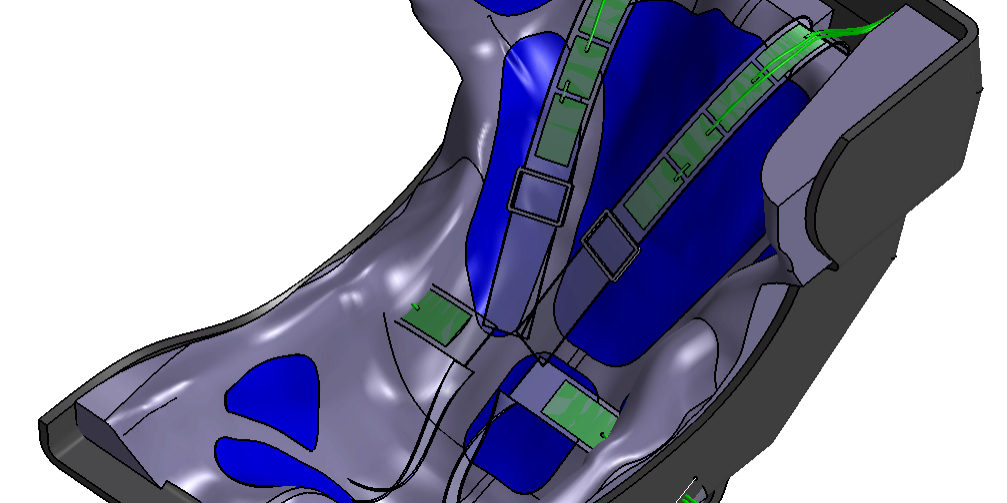
PRO System
The Proportional Rapid Onset (PRO) System allows the seat itself to move independently of the other simulator modules. Situated on an X, Y, Z table, the seat movements can accurately replicate very minor and fast movements that cannot be produced by the main suspension platforms.
For example, under high g-force braking, the driver can be brought closer to the controls and their eye height dropped to simulate the “submarining” effect where the body is compressed. It can also be used to replicate very quick lateral or longitudinal accelerations such as gear changes.
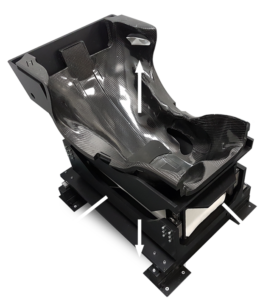
Yaw Platform
The yaw platform is situated at the base of the simulator and is used to simulate lateral movements of the rear end of the vehicle. This is necessary to feel the limits of traction of the rear tyres, which cannot be achieved by solely depending on the visual system. It is only with a good yaw motion system that a driver can consistently drive right at the edge of the tyre grip limits.
Transitioning from one corner to the next is also felt through this module particularly, for example, driving through high speed chicanes.
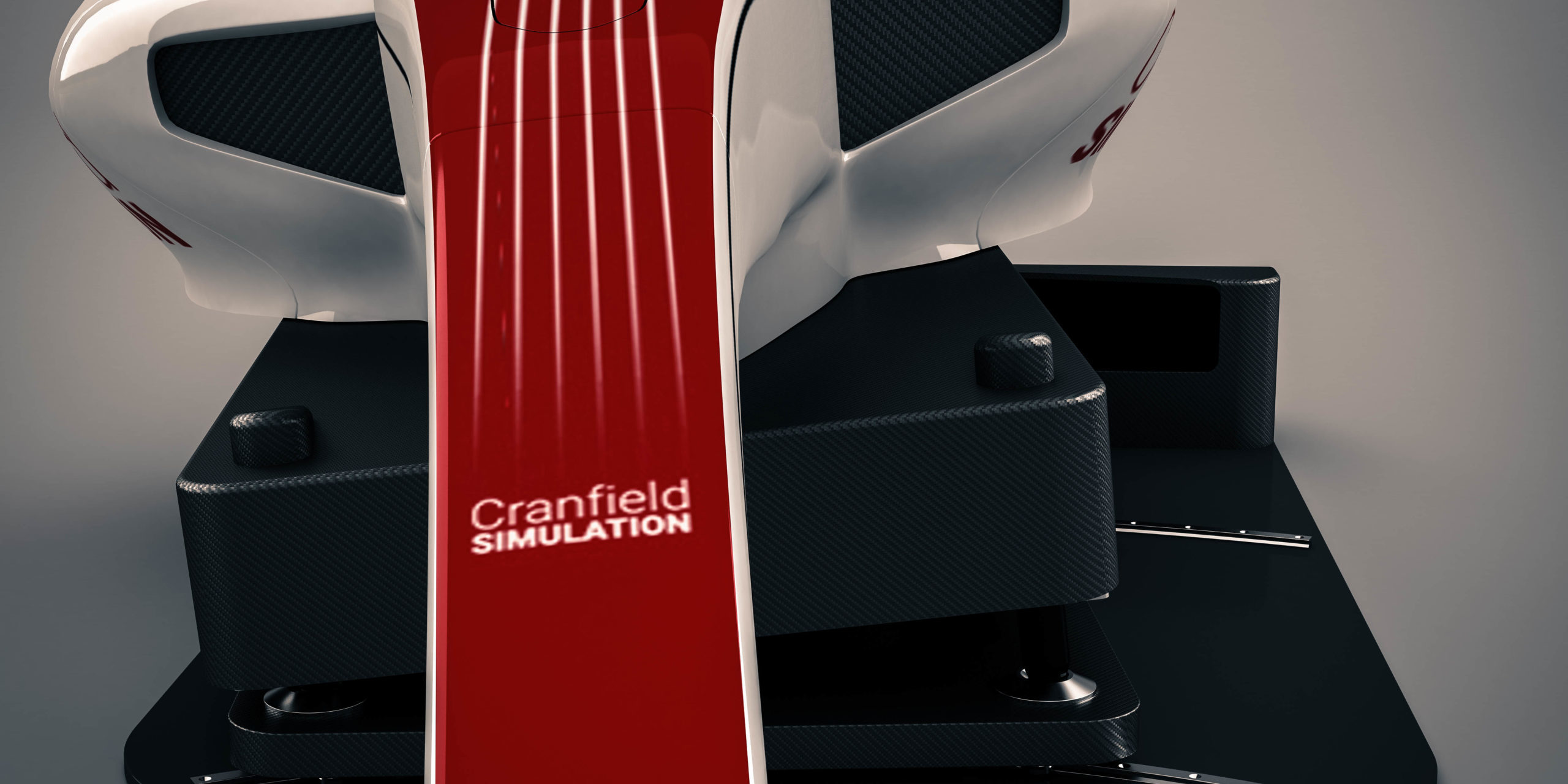
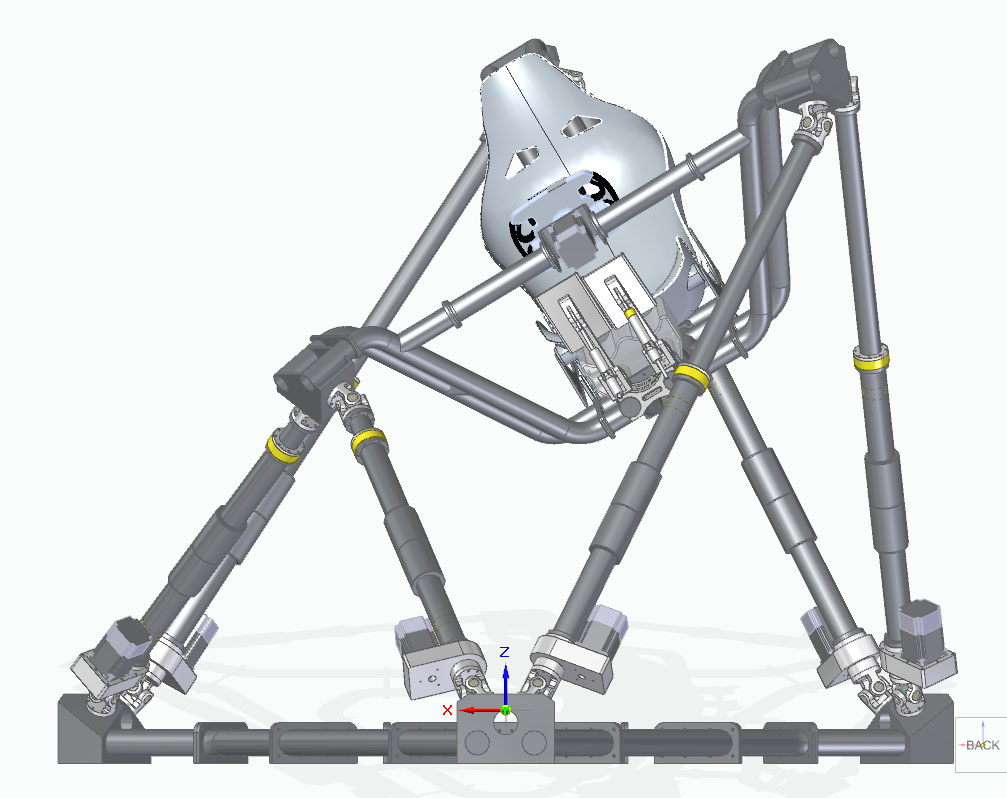
TRADITIONAL METHODS OF SIMULATING MOTION (and why we do things differently)
The most common motion solution is the 6-DoF platform, also known as the ‘hexapod’. These systems were originally designed for civil aircraft applications where slow but large movements of pitch, roll and heave are of importance, but very little lateral or longitudinal motion is required.
In motorsport, the exact opposite of this is true. Racecars are very stiff and are designed to minimize pitch and roll. For this reason, excessive roll and/or pitch is sometimes used in simulators to utilise the gravity to add further to the feeling of lateral and longitudinal acceleration. Not only do these systems provide negative cues, it is also physically limited to simulating 1G and requires high-power electronics to move the whole simulator. It can also be a cause of motion sickness to some users as their inner balance is affected.
Additionally, with a traditional motion platform, a period of deceleration is required following an acceleration cue (washout). In order to avoid a miscue and/or reduce motion sickness, the deceleration has to be conducted at a rate that is undetectable by the user. This drastically increases the necessary room required to correctly simulate accelerations associated with high performance vehicles.
A high-speed corner such as the Parabolica at Monza creates around an average of 3g for 6 seconds in an F1 car. Using kinematic equations of motion, it is possible to calculate it would require a staggering 529.74m of travel to generate this in physical lateral movement for the period of acceleration and deceleration required. This feat is only possible with a huge floorspace by moving the simulator on extremely long rails powered by large and expensive motors. The platform would also have to return to the centre position in time to simulate the next corner of the circuit slowly without generating any negative cues for the user.
Our patented g-cueing system is able to get around this by focusing on somatic (tactile) feedback. As humans, we do not actually possess a sense (touch, taste, smell, hear, sight) to “feel” acceleration or g-forces, but instead use a combination of cues to realize we are accelerating. While vision does play a big part, tactile feedback of the forces through the seat and belts enable us to “feel” changes in acceleration in racing. Using our patented technology, we can simulate these sensations to great accuracy and thus deceive the brain into feeling sustained g-forces. This enables us to simulate higher levels of g-forces indefinitely at a higher fidelity, all in a smaller package and footprint.
FIND THE RIGHT SETUP FOR YOU
Visit: www.axsim.racing